About Us
We Focus on the Production of Perfluoroether Rubber Products
Hongxin FFKM Technology Co., Ltd. was established in February 2022 with a registered capital of 10 million yuan and is located in Su Dongpo District, Meishan City, the hometown of Dongpo. It is a subsidiary of Sichuan Dowhon Group. The company is equipped with 1600 square meters of dust-free workshop and 300 square meters of dust-free R & D center with industrial standard pollution control, a complete dust-free workshop environment can provide the best quality products. For semiconductor customers, we can develop the most advanced perfluoroelastomer rubber to meet the most stringent quality and cleanliness requirements.
View more
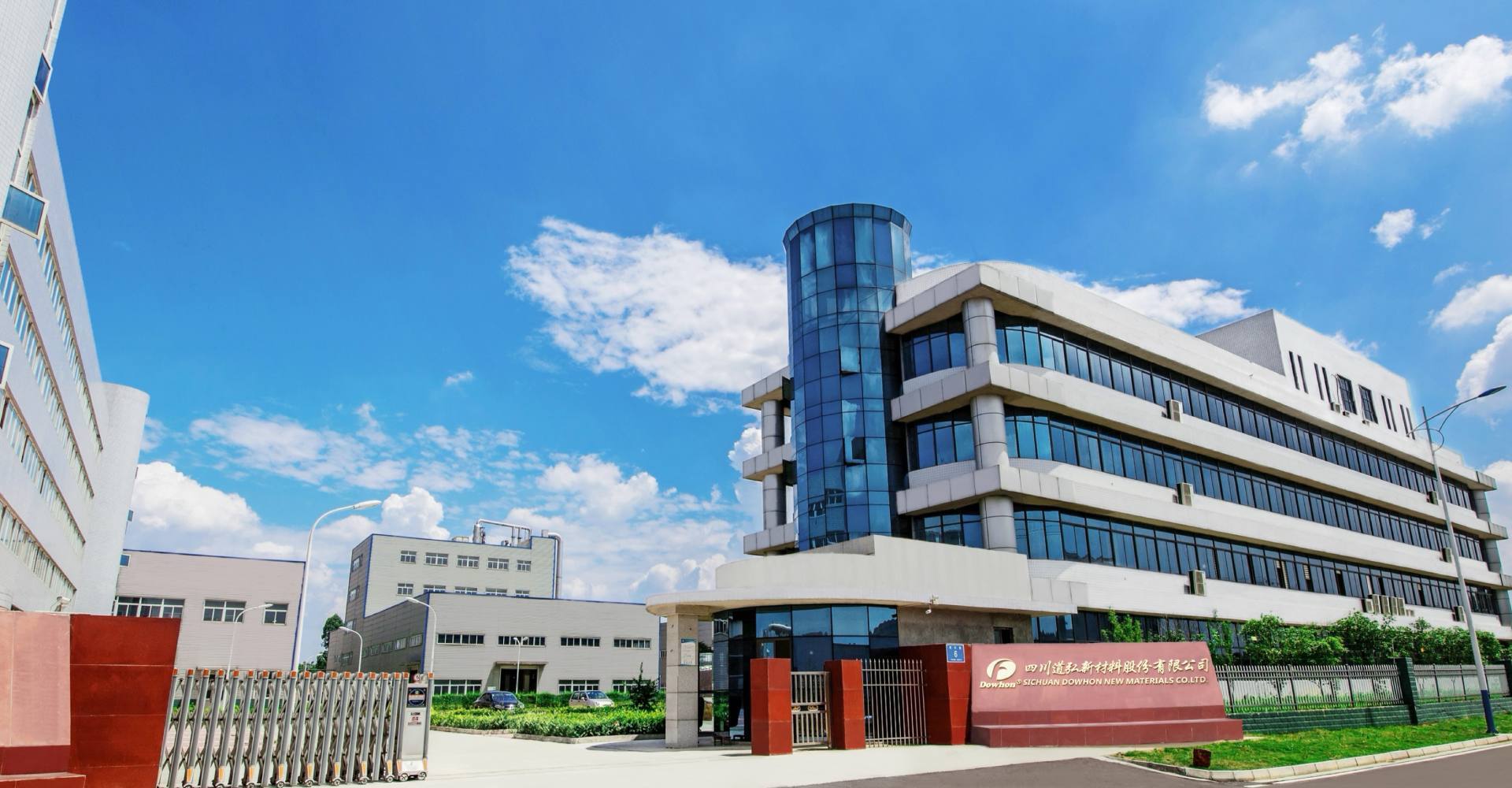
2022
Year
Established in 2022
1600
㎡
Dust-free workshop 1600 ㎡
10
Million Yuan
Registered capital 10 million yuan
300
㎡
Dust-free R & D Center 300 ㎡
FFKM O-ring
FFKM O-ring
FFKM O-ring
FFKM O-ring
FFKM O-ring
FFKM Compound
FFKM Compound
FFKM Compound
FFKM Compound
FFKM Compound
FFKM precompound
FFKM precompound
FFKM precompound
FFKM precompound
FFKM precompound
FFKM Raw Gum
FFKM Raw Gum
FFKM Raw Gum
FFKM Raw Gum
FFKM Raw Gum
Products
Application
Focus on the development and production of Perfluoroelastomer rubber O-rings